Comparing K100 and H13 Steel Alloys
2/10/20241 min read
Introduction:
K100 and H13 are two prominent steel alloys recognized for their exceptional properties.
This thread aims to delve into the characteristics of each alloy, shedding light on their applications.
Composition:
K100: Boasting high carbon and chromium content, ensuring superior wear resistance and hardness.
H13: A hot-work tool steel with a combination of chromium, molybdenum, and vanadium for excellent toughness and heat resistance.
Hardness and Wear Resistance:
K100: Known for outstanding hardness, ideal for applications requiring resistance to wear and abrasion.
H13: Possesses good hardness and wear resistance, suitable for high-temperature applications.
Toughness and Impact Resistance:
K100: Maintains good toughness, allowing it to endure impact without brittle failure.
H13: Offers excellent toughness, particularly at elevated temperatures, making it suitable for hot-working applications.
Applications:
K100: Commonly used in tool and die applications, providing high hardness for precision cutting.
H13: Widely employed in forging and die-casting applications due to its excellent heat resistance.
Machinability:
K100: Machinable, although specialized tools may be required due to its hardness.
H13: Machinable under proper conditions, but its hot-working properties should be considered.
Corrosion Resistance:
K100: Exhibits good corrosion resistance compared to other high-carbon steels.
H13: Moderate corrosion resistance; proper maintenance is essential to prevent rust.
Cost Considerations:
K100: Considered a premium steel alloy, reflecting its unique properties.
H13: Generally more cost-effective compared to premium tool steels like K100.
Conclusion:
In conclusion, the choice between K100 and H13 depends on specific application requirements, temperature conditions, and budget considerations.
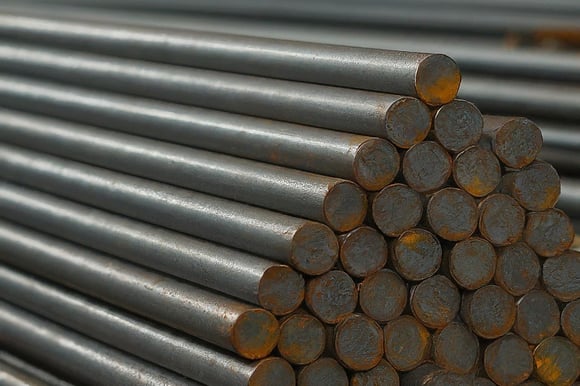
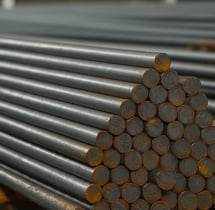
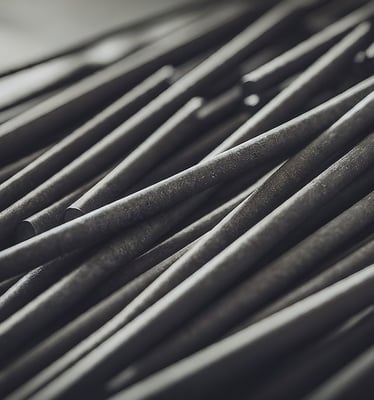
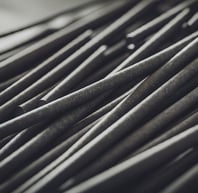
Contacts
info@redeagle.shop